Whiting
General Information:
Chemical formula: CaCO3
Other names: Calcium Carbonate
Sources:
- Omya10 (Australia)
- Crecer (Argentina)
- Kalkspat Bodmer 512 (Switzerland)
- Snowcal 40 (England)
- Vicron 2511 (United States)
Common forms: Found as minerals calcite and aragonite, in chalk, limestone, eggshells, gastropod shells, shellfish skeletons, and pearls
Ceramic Substitutes: wollastonite, frits, food waste shells
Whiting is the main source of calcium (alkaline earth flux) for glazes, it helps produce hard glazes and matts in excess. It is a fine grind of chalk (aragonite - marine shell deposits).
The purest sources are in England, France, and Belgium. China is the world's largest producer of calcium carbonate, followed by the United States and various European countries. India, Japan, and Russia are also significant producers of calcium carbonate.
Limestone, which is the primary source of calcium carbonate, is mined extensively around the world, with major mining sites located in countries like the United States, Australia, and others.
Other sources include marble, calcite ores, and sea shells. Whiting and limestone are not necessarily the same thing; limestone may contain considerable amounts of magnesium (i.e. dolomite) and some suppliers do not distinguish, be sure to ask.
Add byproduct vs primary product info. Whiting is generally inexpensive and there is a large calcium carbonate industry worldwide for non-ceramic uses of this mineral.
The purest sources are in England, France, and Belgium. China is the world's largest producer of calcium carbonate, followed by the United States and various European countries. India, Japan, and Russia are also significant producers of calcium carbonate.
Limestone, which is the primary source of calcium carbonate, is mined extensively around the world, with major mining sites located in countries like the United States, Australia, and others.
Other sources include marble, calcite ores, and sea shells. Whiting and limestone are not necessarily the same thing; limestone may contain considerable amounts of magnesium (i.e. dolomite) and some suppliers do not distinguish, be sure to ask.
Add byproduct vs primary product info. Whiting is generally inexpensive and there is a large calcium carbonate industry worldwide for non-ceramic uses of this mineral.
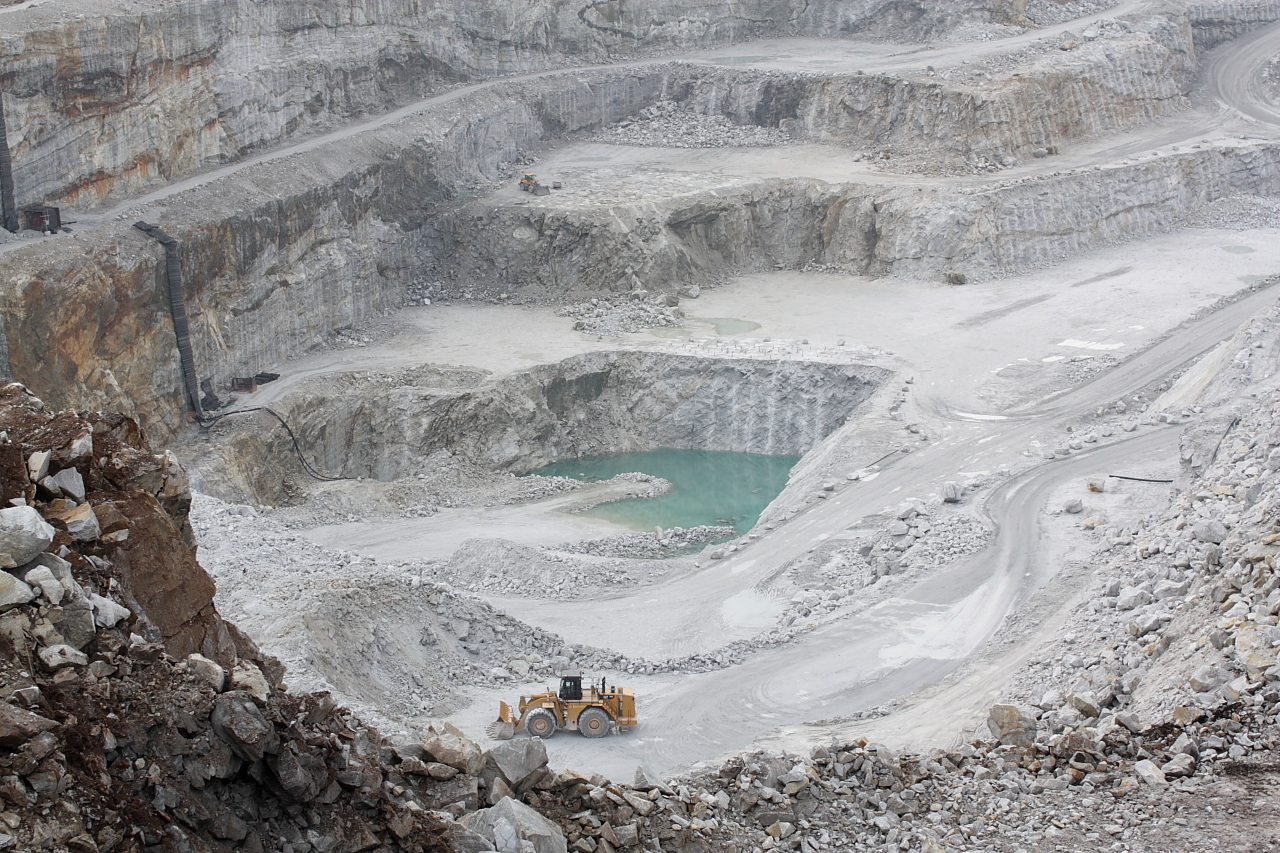
How it’s processed:
The mineral beneficiation processes used in the production of calcium carbonate [in Australia] involve various stages to extract and refine the mineral. These processes include:
According to the search results the precipitation step, where the calcium hydroxide slurry is carbonated to produce calcium carbonate, is the most critical and complex part of the overall calcium carbonate processing.
The precipitated calcium carbonate (PCC) production process begins with quicklime (CaO). The quicklime is mixed with water to form a calcium hydroxide slurry (Ca(OH)2) in an exothermal chemical reaction known as slaking. This slurry is then cooled and transported to a mix tank, where CO2 is added. This carbonates the calcium hydroxide slurry to produce calcium carbonate.
The final step in the PCC production process is to screen the calcium carbonate to remove any off-spec particle sizes. Screen sizes can be as fine as 325 mesh (44μm). The final screened product is then stored in a holding tank until needed.
The end result of this precipitation process is a calcium carbonate product that can be controlled for particle size, surface area, particle shape, and surface chemistry to meet customer specifications. PCC is also whiter and brighter than most naturally occurring calcium carbonate.
- Crushing and Grinding: The calcite ore is crushed into smaller particles and ground into fine powder using crushers and grinding mills
- Flotation: Calcite ores typically contain impurities like metal sulphide, silicate, or other minerals, which are removed through the froth-flotation process using collectors like amines and xanthate collectors
- Calcination: In the manufacturing process of calcium carbonate powder, limestone is heated in a kiln at around 1000°C to produce quicklime (calcium oxide) and carbon dioxide gas
- Slaking and Carbonation: The quicklime is mixed with water to create slaked lime (calcium hydroxide), which is then reacted with carbon dioxide gas to produce calcium carbonate powder
According to the search results the precipitation step, where the calcium hydroxide slurry is carbonated to produce calcium carbonate, is the most critical and complex part of the overall calcium carbonate processing.
The precipitated calcium carbonate (PCC) production process begins with quicklime (CaO). The quicklime is mixed with water to form a calcium hydroxide slurry (Ca(OH)2) in an exothermal chemical reaction known as slaking. This slurry is then cooled and transported to a mix tank, where CO2 is added. This carbonates the calcium hydroxide slurry to produce calcium carbonate.
The final step in the PCC production process is to screen the calcium carbonate to remove any off-spec particle sizes. Screen sizes can be as fine as 325 mesh (44μm). The final screened product is then stored in a holding tank until needed.
The end result of this precipitation process is a calcium carbonate product that can be controlled for particle size, surface area, particle shape, and surface chemistry to meet customer specifications. PCC is also whiter and brighter than most naturally occurring calcium carbonate.
Permaculture Ethics
Earth Care
The mining and processing of calcium carbonate can have various environmental impacts:
Overall, while calcium carbonate plays essential roles in various industries, its mining and processing can have environmental implications such as waste generation, alteration of soil properties, and impacts on aquatic ecosystems. Efforts to mitigate these impacts include exploring mineral carbonation for CO2 sequestration and sustainable mining practices to minimize environmental harm.
- Mining Waste: Mining waste can generate acidic or alkaline leachate with high concentrations of metals and metalloids, posing a risk to the environment 1.
-
Carbon Sequestration: Mineral carbonation, a process that involves the reaction of CO2 with minerals like calcium carbonate, can help reduce CO2 emissions associated with industrial activities like aluminum production5.
-
Soil Properties: Calcium carbonate influences soil properties and is a significant terrestrial carbon store, impacting soil health and ecosystem dynamics2.
-
Water Treatment: Calcium carbonate is used in water treatment processes, which can affect aquatic ecosystems depending on the concentration and disposal methods of the byproducts3.
-
Coastal Sediments: Biological production of calcium carbonate in oceans contributes to coastal sediments through the breakdown of calcareous organisms, influencing coastal erosion and sediment dynamics4.
Overall, while calcium carbonate plays essential roles in various industries, its mining and processing can have environmental implications such as waste generation, alteration of soil properties, and impacts on aquatic ecosystems. Efforts to mitigate these impacts include exploring mineral carbonation for CO2 sequestration and sustainable mining practices to minimize environmental harm.
People Care
There appear to be some potential human rights and workers' rights issues associated with the calcium carbonate industry:
Overall, the search results suggest that the large-scale mining and extraction of calcium carbonate, as well as its use in carbon offset schemes and concentration in certain developing regions, may be linked to human rights, land rights, and workers' rights issues in the calcium carbonate industry. More transparency and stronger safeguards appear to be needed to address these concerns.134
- The first search result discusses concerns about the carbon markets system, which can allow polluters to offset their emissions by buying carbon credits from projects involving Indigenous Peoples' lands. This suggests that the exploitation of calcium carbonate resources on Indigenous lands may be linked to violations of their land rights and lack of free, prior and informed consent.1
- The search results indicate that much of the calcium carbonate used in industry is exploited from mines and quarries.3 This reliance on mining operations raises concerns about potential labor rights issues, such as poor working conditions, low wages, or the use of child labor in some regions, particularly in developing countries.34
- The search results mention that the exploitation of calcium carbonate for plastic industry applications is concentrated in countries like China, Vietnam, and Malaysia.34 This geographic concentration may indicate a lack of robust labor protections and environmental regulations in these areas, which could lead to exploitation of workers and communities.34
Overall, the search results suggest that the large-scale mining and extraction of calcium carbonate, as well as its use in carbon offset schemes and concentration in certain developing regions, may be linked to human rights, land rights, and workers' rights issues in the calcium carbonate industry. More transparency and stronger safeguards appear to be needed to address these concerns.134
Other Uses for Whiting:
- Construction industry - Used as a building material, limestone aggregate for road building, an ingredient in cement, and as the starting material for preparing builders' lime.
- Iron and steel production - Added to blast furnaces to help purify iron ore by forming a slag with impurities.
- Medical and Pharmaceutical Uses - Used as an inert filler for tablets, in toothpaste, as a calcium supplement, antacid, and phosphate binder, as well as a food preservative.
- Agricultural Uses - Used as a soil conditioner, calcium fertilizer, and livestock feed additive to improve pH, provide essential nutrients, and promote animal health.
- Oil industry - Added to drilling fluids as a weighting material and to help seal the borehole.
FOOTNOTES
- https://www.perplexity.ai/search/what-are-non-aRr6Tp3sTtepvzaPOZ598Q
- https://digitalfire.com/material/calcium+carbonate
- https://glazy.org/materials/15457
- https://fillplas.com/calcium-carbonate-caco3-and-industrial-applications/
- https://tankymineral.com.vn/whiting-calcium-carbonate-in-ceramic-342569
- https://www.mnclay.com/AddToCart2.aspx?ProductGroup=CALCAW
Nepheline Syenite
General Information:
Chemical formula: K2O•3Na2O•4Al2O3•9SiO2
Other names: Feldspathic rock
Sources:
- Nepheline Syenite Spectrum A270 (Canada)
- Spectrum N45 (Norway)
Common forms:
The common forms or varieties of nepheline syenite include cancrinite nepheline-syenite, eudialyte-bearing nepheline-syenite, foyaite, litchfieldite, malignite, pegmatitic nepheline syenite, pseudoleucite syenite, alkali-feldspar nepheline-syenite, and apgaitic nepheline-syenite. 12
Ceramic Substitutes: soda feldspar
A feldspathic mineral mined in Canada and Norway. Nepheline syenite is a valuable material in ceramics, acting as an efficient flux while providing beneficial properties like whiteness, low firing temperatures, and stable thermal expansion to clay bodies and glazes.
Although feldspar-like in its chemistry, mineralogically it is an igneous rock combination of nepheline, microcline, albite and minor minerals like mica, hornblende and magnetite. It is found in Canada, India, Norway and USSR. This material has a big advantage over feldspar: It does not contain quartz.
Nepheline syenite is widely used in clay bodies. It acts as a flux, lowering the maturing temperature required for vitrification. In vitreous china bodies, it forms a vitreous mass with free silica, increasing cast rate and density. Nepheline syenite contributes high alumina without associated free silica, stabilizing the expansion of the fired body. Typical usage levels range from 25-50% in cone 4-6 porcelain bodies.3 4 5
The unique properties of nepheline syenite make it valuable in glazes as well. It serves as an efficient flux, melting at lower temperatures than feldspars 6 8, which expands the working range of glazes. Its sodium content can help prevent crazing or cracking in glazes.35 When used in larger amounts, nepheline syenite can act as an opacifier, giving glazes a milky appearance. However, being slightly soluble, it can cause issues like gelling in glaze slurries over time if not properly deflocculated.3
Beyond its fluxing abilities, nepheline syenite imparts whiteness to clay bodies and glazes. Unlike some feldspars, it does not contain free silica or quartz, improving the fired product's expansion stability. Lower amounts are needed compared to feldspars due to its high alkali content relative to silica. These properties make nepheline syenite a valuable material for achieving desired characteristics in ceramic products.34
Although feldspar-like in its chemistry, mineralogically it is an igneous rock combination of nepheline, microcline, albite and minor minerals like mica, hornblende and magnetite. It is found in Canada, India, Norway and USSR. This material has a big advantage over feldspar: It does not contain quartz.
Nepheline syenite is widely used in clay bodies. It acts as a flux, lowering the maturing temperature required for vitrification. In vitreous china bodies, it forms a vitreous mass with free silica, increasing cast rate and density. Nepheline syenite contributes high alumina without associated free silica, stabilizing the expansion of the fired body. Typical usage levels range from 25-50% in cone 4-6 porcelain bodies.3 4 5
The unique properties of nepheline syenite make it valuable in glazes as well. It serves as an efficient flux, melting at lower temperatures than feldspars 6 8, which expands the working range of glazes. Its sodium content can help prevent crazing or cracking in glazes.35 When used in larger amounts, nepheline syenite can act as an opacifier, giving glazes a milky appearance. However, being slightly soluble, it can cause issues like gelling in glaze slurries over time if not properly deflocculated.3
Beyond its fluxing abilities, nepheline syenite imparts whiteness to clay bodies and glazes. Unlike some feldspars, it does not contain free silica or quartz, improving the fired product's expansion stability. Lower amounts are needed compared to feldspars due to its high alkali content relative to silica. These properties make nepheline syenite a valuable material for achieving desired characteristics in ceramic products.34
How it’s processed:
Nepheline syenite is typically processed through the following main steps:
The key aims are to remove iron-bearing impurities to very low levels (typically <0.1% Fe2O3), concentrate the nepheline and feldspar minerals, and produce a sized product with high alumina (typically >23% Al2O3) and alkali (>14% Na2O+K2O) content suitable for glass, ceramics and other applications.
- Crushing and Milling: The nepheline syenite ore is first crushed and then milled to reduce the particle size, typically to a range of 420 to 75 μm for glass applications and even finer sizes like 75, 53, and 38 μm for ceramic applications. 7
- Magnetic Separation: After comminution, magnetic separation is employed to remove iron-bearing minerals like magnetite and hematite present in the ore.7 This is crucial as the iron content should not exceed 0.1% Fe2O3 for glass-grade nepheline syenite.
- Flotation: Some processes also employ flotation techniques after or in combination with magnetic separation to further remove impurities and concentrate the nepheline and feldspar minerals.9 8
- Leaching: Certain processes utilize leaching, typically with acids like oxalic acid, to remove residual iron and other impurities from the magnetic separation/flotation concentrates to meet strict iron specifications for glass and ceramics applications.7 9
- Demagnetization: The final concentrates may undergo demagnetization to remove any residual magnetic particles.6
- Size Classification:The processed nepheline syenite concentrate is classified into specific size fractions (e.g. -36+200 mesh) as required for different end-use industries like glass, ceramics, paints etc.6
The key aims are to remove iron-bearing impurities to very low levels (typically <0.1% Fe2O3), concentrate the nepheline and feldspar minerals, and produce a sized product with high alumina (typically >23% Al2O3) and alkali (>14% Na2O+K2O) content suitable for glass, ceramics and other applications.
Permaculture Ethics
Earth Care
There are several potential environmental concerns associated with mining and processing nepheline syenite:
While nepheline syenite itself may not be inherently hazardous, the mining, processing, and disposal of large volumes of the rock and its waste products can lead to various environmental impacts. Proper environmental assessments, mitigation measures, and waste management practices are crucial to minimize these concerns.
- Land disturbance and reforming: Mining of nepheline syenite, like any mining activity, can lead to significant land disturbance and reforming of the landscape. 9 This can disrupt natural habitats and ecosystems.
- Solid Waste Generation: The mineral processing of nepheline syenite involves various steps like comminution, magnetic separation, and flotation, as described above. These processes can generate solid waste in the form of tailings, which may contain residual valuable minerals or potentially harmful substances.
- Water consumption and pollution: Mining and quarrying activities associated with nepheline syenite have the potential to cause water pollution.8 This could arise from discharge of mine effluents, runoff from waste rock piles, or leaching of contaminants into groundwater. While not explicitly mentioned, mineral processing operations often involve water usage for various purposes, such as slurry preparation, flotation, and washing. This can lead to high water consumption.
- Air pollution from dusting: The nepheline syenite tailings or mining waste can be a source of air pollution due to dusting, posing a threat to the environment.10 Fine particulate matter can get airborne and contribute to air quality issues.
- Environmental risks from tailings: The nepheline-containing tailings or waste from mining and processing can pose real environmental threats if not properly managed. 10 These waste materials need to be contained or stabilized to prevent air and water pollution.
- Rejected mining proposals due to eclogical risks: The search results cite a specific example where a proposed nepheline syenite mining project in Armenia was rejected due to potential ecological risks during the Soviet era, though it is being revisited now.8
While nepheline syenite itself may not be inherently hazardous, the mining, processing, and disposal of large volumes of the rock and its waste products can lead to various environmental impacts. Proper environmental assessments, mitigation measures, and waste management practices are crucial to minimize these concerns.
People Care
While the search results do not explicitly mention harm caused to humans from nepheline syenite exploitation, the use of hazardous chemicals, high-temperature processes, and potential occupational risks during mining and processing could pose risks if not properly managed and regulated. However, more specific information on the safety aspects and potential human impacts is not provided.
Other Uses for Nepheline Syenite:
The ceramics industry is one of the main consumers of Nepheline syenite though others include the glass, paint, coatings and construction industries, taking advantage of its properties as a flux, filler and whitening agent.
- Glass Industry: Acts as alumina source, increases resistance, durability, lowers melting point, reduces fuel consumption, requires specific size range and low iron content.
- Paint, Coatings, Adhesives, Plastics and Inks: Performance enhancer, provides brightness, tint retention, weatherability, color, sheen uniformity, chemical resistance, durability. 8
FOOTNOTES
- https://www.alexstrekeisen.it/english/pluto/nephelinesyenite.php
- https://www.mindat.org/min-48350.html
- https://digitalfire.com/material/nepheline%2Bsyenite
- https://ceramics.sibelcotools.com/sanitaryware/vitreous-china/nepheline-syenite/
- https://www.midsouthceramics.com/product/nepheline-syenite/
- https://www.linkedin.com/pulse/nepheline-syenite-market-report-industry-6efhf
- https://www.ecolur.org/en/news/mining/14219/
- https://www.quarzwerke.com/en/products/high-performance-fillers/nepheline-syenite
- https://modernusa.tech/nepheline-syenite-rocks/
- https://www.mdpi.com/2075-163X/11/7/734
- https://www.raco.cat/index.php/afinidad/article/download/408489/50677
- https://www.grandviewresearch.com/industry-analysis/nepheline-syenite-market
- https://www.transparencymarketresearch.com/feldspar-nepheline-syenite-market.html
Silica
General Information:
Chemical formula: SiO2 (silicon dioxide)
Other names: crystalline Silica (quartz), silicon dioxide (SiO2), sand, silica sand, flint, silica flour, quartz sand
Sources:
- Holcim - Silica 350 (Australia)
- Silice 200 (France)
- Sil-co-sil (United States)
- Arkansas Whetstone/Novacite (United States)
- Min-U-Sil 40 (United States)
- Solargil Silice (France)
- Bangalore Quartz (India)
-
Silica Teresa (Cuba)
Common forms:
The common geological forms of silica are quartz, cristobalite, tridymite, coesite, stishovite, lechatelierite, and different varieties of amorphous or non-crystalline silica.1
Ceramic Substitutes: soda feldspar
Silica/Quartz 2 is the most abundant mineral on earth, it is the main crystalline mineral form of silica (SiO2). Natural deposits of relatively pure quartz are plentiful and grains of it are found in many other types of rocks and in most silts, soils and clay. White or milky quartz is an opaque white, greasy-looking, sharply angular very hard rock. Pure quartz melts at 1713C, far beyond the range of an average pottery or industrial production kiln.
From a theoretical perspective, quartz is a mineral. However, in ceramics, it is also considered a material, often simply called "silica" (however original container bags often label it as "ground quartz"). Huge quantities of quartz powder are used in ceramic bodies and glazes. In bodies the quartz particles most often remain unchanged in the fired matrix, behaving as an embedded aggregate. They act as a "skeleton" in porcelain bodies. They raise the thermal expansion and make it easier to fit glazes. However, in glazes, the quartz particles dissolve in the glass and become a part of its chemical structure (thus the original properties of the quartz are gone, giving way to the new physical presence of the glass). The term "silicate" refers to minerals or fired materials where SiO2 predominates in the inventory or molecules that make up its structure. Kaolin is a silicate. In kaolin crystals, there are 2 molecules of SiO2 for every one of Al2O3. They combine chemically to form the familiar flat, stop-sign shape.
Quartz is the mineral form of silica powder used in ceramic glazes and clay bodies. It is the mineral that silica "wants to be" when cooled from molten to solid. Unlike silica glass, the quartz phase of silica is subject to inversion and accompanying volume and form change when fired through 573C. Room temperature quartz is called alpha quartz, beta quartz exists only above 573C.
Quartz sand is often used in bodies as grog for texture and to increase thermal expansion. Quartz of very fine particle size (-400 mesh) will typically enter the feldspathic melt or convert to cristobalite during firing if fluxes are lacking, coarse powdered grades help to 'squeeze' glazes into fit. Intermediate sizes (200-300 mesh) seem to be best however, since their greater surface area exerts more compressive squeeze per unit.
Quartz is also used in agriculture, paving, brick and tile, concrete, cleansers, foundry casting, paint, glass, soaps, fiberglass, electronics, plaster, sandblasting, industrial effluent filtration, drinking water filtration, hazardous waste control.
From a theoretical perspective, quartz is a mineral. However, in ceramics, it is also considered a material, often simply called "silica" (however original container bags often label it as "ground quartz"). Huge quantities of quartz powder are used in ceramic bodies and glazes. In bodies the quartz particles most often remain unchanged in the fired matrix, behaving as an embedded aggregate. They act as a "skeleton" in porcelain bodies. They raise the thermal expansion and make it easier to fit glazes. However, in glazes, the quartz particles dissolve in the glass and become a part of its chemical structure (thus the original properties of the quartz are gone, giving way to the new physical presence of the glass). The term "silicate" refers to minerals or fired materials where SiO2 predominates in the inventory or molecules that make up its structure. Kaolin is a silicate. In kaolin crystals, there are 2 molecules of SiO2 for every one of Al2O3. They combine chemically to form the familiar flat, stop-sign shape.
Quartz is the mineral form of silica powder used in ceramic glazes and clay bodies. It is the mineral that silica "wants to be" when cooled from molten to solid. Unlike silica glass, the quartz phase of silica is subject to inversion and accompanying volume and form change when fired through 573C. Room temperature quartz is called alpha quartz, beta quartz exists only above 573C.
Quartz sand is often used in bodies as grog for texture and to increase thermal expansion. Quartz of very fine particle size (-400 mesh) will typically enter the feldspathic melt or convert to cristobalite during firing if fluxes are lacking, coarse powdered grades help to 'squeeze' glazes into fit. Intermediate sizes (200-300 mesh) seem to be best however, since their greater surface area exerts more compressive squeeze per unit.
Quartz is also used in agriculture, paving, brick and tile, concrete, cleansers, foundry casting, paint, glass, soaps, fiberglass, electronics, plaster, sandblasting, industrial effluent filtration, drinking water filtration, hazardous waste control.

How it’s processed:
Silica is processed for ceramic use through several key stages:
The high purity, controlled particle size, and thermal stability of the processed silica sand make it suitable as a filler material in ceramic bodies, providing strength, reducing shrinkage, and promoting vitrification during firing of ceramic products like porcelain, tiles, and refractories.
- Crushing and Grinding: The raw silica rock or sand is first crushed using jaw or impact crushers to reduce the particle size. This is followed by grinding in a ball mill or other grinding equipment to further reduce the silica to a fine powder consistency suitable for ceramic applications.3
- Purification: Since natural silica contains impurities like iron oxides, alumina, and other minerals, it needs to be purified. Common purification methods include:
1) Washing and scrubbing to remove surface contaminants and clay particles.
2) Magnetic separation to remove iron-bearing impurities.
3) Froth flotation to separate quartz (SiO2) from other mineral impurities based on their surface properties.
4) Acid leaching with hydrochloric or sulfuric acid to dissolve metallic impurities.
The purification steps aim to increase the silica content to 99% or higher for use in ceramics and other high-purity applications.3
- Sizing and Drying: After purification, the silica is sized by screening or air classification to obtain the desired particle size distribution for ceramic bodies. Finally, the sized silica sand is dried in rotary or fluid bed dryers to remove moisture before being used in ceramic manufacturing processes.3
The high purity, controlled particle size, and thermal stability of the processed silica sand make it suitable as a filler material in ceramic bodies, providing strength, reducing shrinkage, and promoting vitrification during firing of ceramic products like porcelain, tiles, and refractories.
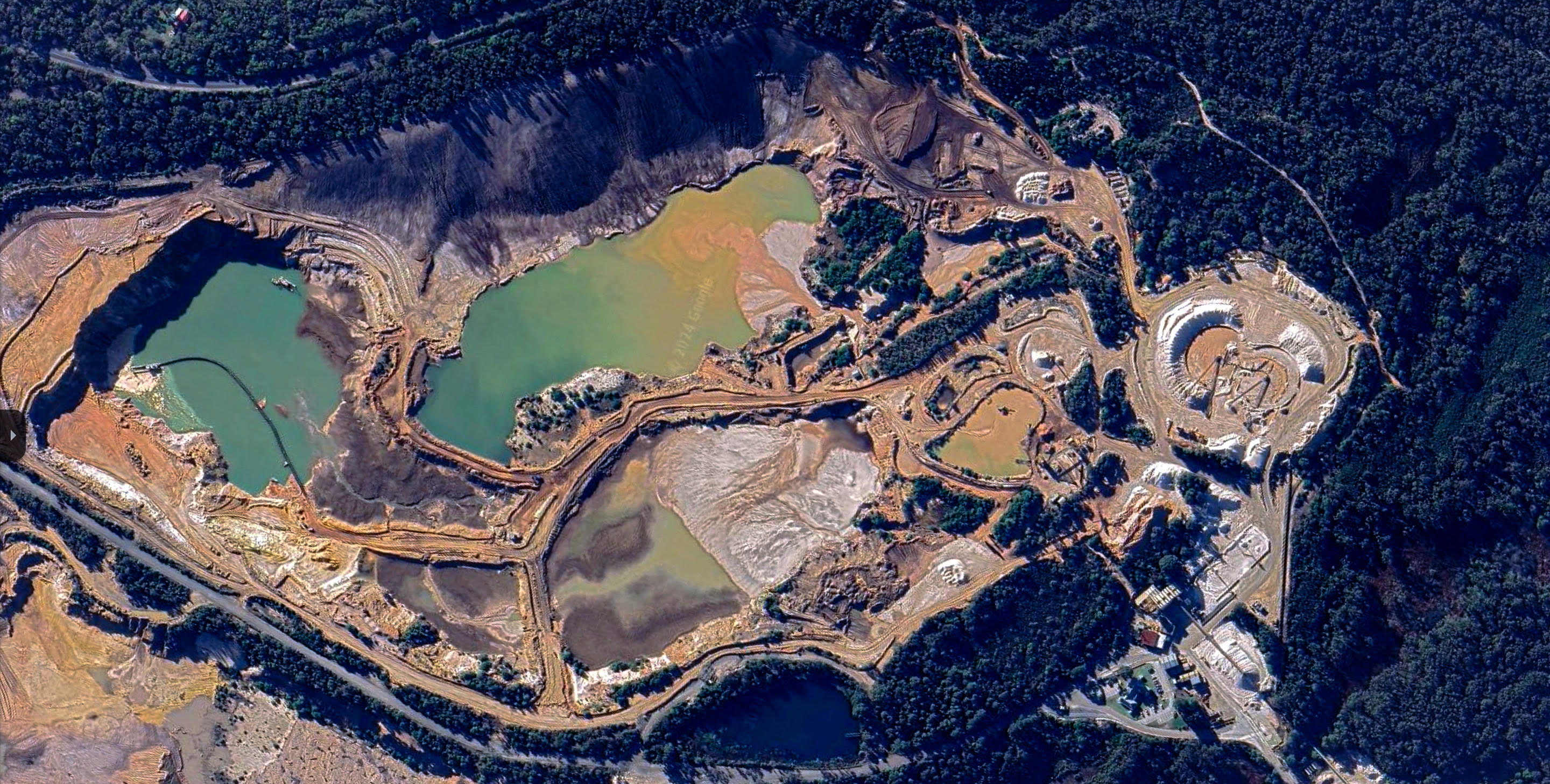
Permaculture Ethics
Earth Care
- Water Pollution: During illegal mining and refining of silica sand, excessive amounts of mud, silt, and sand can accumulate, causing water pollution in natural water bodies.4
Water is a crucial element in processing and refining silica sand. The use and potential mismanagement of water resources during these processes can lead to water pollution.5
-
Ecosystem Loss and Biodiversity Impact: Silica sand extraction often involves the destruction of local ecosystems, including natural habitats and aquatic systems, which can have a devastating impact on biodiversity.6
Open-cast silica mining can cause great damage to forests and biodiversity, as highlighted in the case of the Shankargarh region in India.5
-
Air Pollution: Silica sand extraction and processing operations can release fine silica particles into the air, which can be harmful to human health and the environment.6
-
Energy Consumption and Carbon Footprint: The extraction and processing of silica sand require significant amounts of energy, which can increase the operation's carbon footprint and contribute to climate change.6
- Atom Economy and Resource Efficiency: The dry process of silica production via flame pyrolysis has a lower atom economy (29%) compared to the wet sodium silicate process. This increases the amount of precursor (silicon tetrachloride) required per unit of silica produced, leading to higher environmental impacts.7
The search results emphasize the need for sustainable solutions, such as ecosystem restoration, energy efficiency, emission control, and recycling/reuse of silica sand, to mitigate these environmental impacts and promote responsible silica extraction and processing.
People Care
The mining, extraction, and processing of silica, especially crystalline silica, pose significant health risks to workers and communities exposed to silica dust. Prolonged inhalation of respirable crystalline silica particles can lead to silicosis, a debilitating lung disease. This risk is particularly high in the mining of silica. Additionally, silica extraction and processing can release fine particles into the air and water, posing health risks to surrounding communities and causing environmental pollution. To address these risks, proper control measures such as ventilation systems and personal protective equipment must be implemented. Furthermore, it is important that these protection procedures continue to be evaluated. In 2016, the U.S. Occupational Safety and Health Administration (OSHA) determined that workers exposed to respirable crystalline silica at previous permissible exposure limits faced a significant risk of developing silicosis and other respiratory diseases, necessitating stricter regulations to protect worker health and safety. 10
Workers have fundamental rights to safe working conditions, health protection, information, personal protective equipment, and medical surveillance to mitigate the harmful effects of silica exposure and uphold their well-being.
Workers have fundamental rights to safe working conditions, health protection, information, personal protective equipment, and medical surveillance to mitigate the harmful effects of silica exposure and uphold their well-being.
Other Uses for Silica:
Silica is used in various industries beyond ceramics. Here are some of the key sectors that utilise silica:
The search results highlight that silica's versatile properties make it an essential raw material across various industries, from glass and ceramics to metallurgy, chemicals, construction, and emerging applications in renewable energy technologies.
- Glass Industry: The main use of silica is for flat and container glass manufacture, with around 60% of each glass batch being silica sand.11 Silica is a crucial raw material for producing different types of glass products.
- Foundry Industry: Silica sand is bonded with synthetic resins to make moulds and cores for casting metals in metal foundries.11 The high melting point and thermal stability of silica make it suitable for foundry applications.
- Oil and Gas Industry: Well-rounded silica sand is used as a proppant to prop open fissures in reservoir rocks during hydraulic fracturing operations, improving permeability for oil and gas extraction.11
- Metallurgical Industry: Lump silica (quartzite) is used as a flux in metal smelting processes and as a raw material for the manufacture of ferrosilicon alloys.11
- Chemical Industry: Silica is the raw material for manufacturing various silicon compounds such as silicones, silanes, and high-purity silicon metal used in semiconductors.11
- Construction Industry: While not explicitly mentioned, silica sand is commonly used in the production of concrete, mortars, and other construction materials.
- Abrasives Industry: Silica sand is used in sandblasting and other abrasive applications due to its hardness and angular particle shape.11
- Filtration Industry: Silica is used in water filtration systems, leveraging its chemical and physical properties.11
- Renewable Energy Industry: As mentioned in 12, silica has a growing profile in the renewable energy sector, particularly in the manufacture of photovoltaic cells for solar panels.
The search results highlight that silica's versatile properties make it an essential raw material across various industries, from glass and ceramics to metallurgy, chemicals, construction, and emerging applications in renewable energy technologies.
FOOTNOTES
- https://worksafe.nt.gov.au/safety-and-prevention/crystalline-silica-and-silicosis
- https://digitalfire.com/mineral/quartz
- https://www.ftmmachinery.com/blog/silica-sand-processing-plant.html
- https://www.researchgate.net/publication/289570461_Impact_of_silica_mining_on_environment
- https://academicjournals.org/journal/JGRP/article-full-text-pdf/915EC0C53587
- https://www.geoterradominicana.com/en/articles/the-environmental-impact-of-silica-sand-extraction-and-sustainable-solutions/
- https://pubs.rsc.org/en/content/articlehtml/2023/gc/d2gc01433e
- https://www.mdpi.com/2071-1050/8/1/11
- https://journals.lww.com/imsp/fulltext/2023/14040/early_diagnosis_and_development_of_referral_system.7.aspx
- https://www.federalregister.gov/documents/2016/03/25/2016-04800/occupational-exposure-to-respirable-crystalline-silica
- https://www.energymining.sa.gov.au/industry/minerals-and-mining/mineral-commodities/silica
- https://www.australianresourcesandinvestment.com.au/2022/11/25/the-precise-world-of-silica/
Gerstely Borate
General Information:
Chemical formula: 2CaO Na2O 3B2O3 7H2O
Other names: Colemanite, Calcium Borate, Borocalcite
Sources:
- Gerstley Borate (United States)
Common forms:
Mineralogically it is a combination of colemanite, ulexite and high plasticity clay (likely hectorite). 1
Ceramic Substitutes: Colemanite, Ulexite, Gillespie Borate, and boron frits.
Gerstley Borate supplies B2O3, CaO, other fluxes, SiO2, and Al2O3. Gerstley borate is a calcium borate ore containing the mineral Ulexite, along with accessory minerals such as Bentonite, Colemanite, and Probertite. Gerstley borate was formed in marshes and drying lake basins during the Miocene (10 million years ago). Gerstley borate is named after James Gerstley, former managing director of Borax Consolidated Ltd. It is manufactured by U.S. Borax and Chemical Corp.; the mine is located near Death Valley, CA.
The melting behavior of ulexite and colemanite is quite different, the unusual early melting behavior Gerstley Borate exhibits this, it suddenly implodes to a brown opaque melt (because of the earlier fluxing of ulexite) which later turns transparent (when the colemanite joins in). It begins to melt between 1550F and 1600F and is a clear amber glass by 1750F and ultraclear and glossy by cone 06 (Ulexite melts better but it is not commonly in use in ceramics). It has thus been a staple among potters for many years. 50% or more can be found in many cone 06-02 glazes and 30% is common in cone 6 glazes. Gerstley Borate is also very plastic and thus suspends and hardens glazes as they dry.
The US Borax mine in Boron, California was closed in 2000 and remaining stocks were to be depleted in 2-3 years. There was alarm across the ceramic community in North America leading up to and after the closure (because Gerstley Borate formed the basis of so many glazes). However, in June 2011, the supplier, Laguna Clay, announced that there was again a large supply still available (from an unused stockpile). That lasted until 2022 when rumours arose that it would become permanently unavailable.
The lower the percentage of Gerstley Borate in a glaze recipe the more practical it is to just replace it with a substitute (like Gillespie Borate). But when the proportion gets higher the best approach to finding an alternative is to use glaze chemistry to substitute other material to source the boron(B2O3). Frits, for example, are a less volatile alternative source for B2O3, more consistent and reliable and do not flocculate or gel the glaze as Gerstley Borate does. However, no available frit contains as much B2O3 as Gerstely Borate, and so, in some cases it is not possible to source sufficient B2O3 for existing glaze recipes.
The melting behavior of ulexite and colemanite is quite different, the unusual early melting behavior Gerstley Borate exhibits this, it suddenly implodes to a brown opaque melt (because of the earlier fluxing of ulexite) which later turns transparent (when the colemanite joins in). It begins to melt between 1550F and 1600F and is a clear amber glass by 1750F and ultraclear and glossy by cone 06 (Ulexite melts better but it is not commonly in use in ceramics). It has thus been a staple among potters for many years. 50% or more can be found in many cone 06-02 glazes and 30% is common in cone 6 glazes. Gerstley Borate is also very plastic and thus suspends and hardens glazes as they dry.
The US Borax mine in Boron, California was closed in 2000 and remaining stocks were to be depleted in 2-3 years. There was alarm across the ceramic community in North America leading up to and after the closure (because Gerstley Borate formed the basis of so many glazes). However, in June 2011, the supplier, Laguna Clay, announced that there was again a large supply still available (from an unused stockpile). That lasted until 2022 when rumours arose that it would become permanently unavailable.
The lower the percentage of Gerstley Borate in a glaze recipe the more practical it is to just replace it with a substitute (like Gillespie Borate). But when the proportion gets higher the best approach to finding an alternative is to use glaze chemistry to substitute other material to source the boron(B2O3). Frits, for example, are a less volatile alternative source for B2O3, more consistent and reliable and do not flocculate or gel the glaze as Gerstley Borate does. However, no available frit contains as much B2O3 as Gerstely Borate, and so, in some cases it is not possible to source sufficient B2O3 for existing glaze recipes.
How it’s processed:
Gerstely Borate is processed for ceramic use through:
- Milling and Sieving: Gerstley Borate was first crushed and milled into a fine powder form. It was then sieved to remove any impurities or coarse particles, ensuring a consistent particle size distribution suitable for glaze formulation.
- Fritting: Sometimes, Gerstley Borate was pre-fritted (melted into a glass) before being added to glazes. This involved melting it along with other raw materials in a furnace, quenching the molten glass in water to form a frit, and then milling the frit into a powder. Fritting helped make the boron more insoluble and prevented defects caused by soluble boron compounds.
Permaculture Ethics
Earth Care
For mines primarily focused on extraction, grinding, and sieving activities, like the former Gerstley Borate mine operated by U.S. Borax (now Rio Tinto) in Boron, California, the key environmental concerns and remediation techniques include:
- Air Pollution: The mining process involving drilling, blasting, excavation, crushing, grinding, sieving, and transportation of ore generates large amounts of dust and particulate matter, contributing to air pollution if not properly controlled.
Remediation: Implementing dust suppression systems, enclosures, and air filtration systems to capture and minimize airborne particulates from processing activities.
- Water Pollution: Runoff from mining and processing areas can potentially contaminate surface and groundwater sources with suspended solids, chemicals used in mineral processing, and leached heavy metals or toxins from exposed rocks and tailings if not properly contained.
Remediation: Proper management of surface water runoff, treatment of wastewater before discharge, and prevention of leachate seepage into groundwater through containment and lining systems.
- Soil Contamination: Residual rock slurries, tailings, leakage of chemicals used in mineral processing, and dust deposition can lead to soil contamination in and around the mining and processing areas if not managed properly.
Remediation: Removing and treating contaminated soil, capping or covering tailings and waste rock piles to prevent leaching, and revegetation efforts to stabilize disturbed areas.
- Land Disturbance and Habitat Loss: While the footprint may be smaller than open-pit mines, extraction, processing, and waste disposal activities can still result in land disturbance, removal of topsoil and vegetation, and loss of natural habitats for local flora and fauna.
Remediation: Minimizing the mining and processing footprint, revegetation efforts, and habitat restoration measures to the extent possible after mine closure.
- Landscape Alteration and Visual Impact: The mining and processing facilities, waste rock piles, and tailings impoundments can alter the natural landscape and have visual impacts on the surrounding area.
Remediation: Proper site planning, contouring, and revegetation efforts to minimize visual impacts and integrate the site with the surrounding landscape after closure.
- Ecosystem Disruption: Deforestation, erosion, sedimentation in water bodies, and destruction of natural habitats due to mining and processing activities can disrupt local ecosystems and biodiversity.
Remediation: Implementing measures to minimize disturbance, protect sensitive areas, and restore ecosystems through revegetation and habitat restoration efforts after closure.
People Care
The 1974 Borax strike was a major labor dispute that took place at the US Borax mine in Boron, California, involving nearly 900 miners. Here are the key details about this strike:
The 1974 Borax strike was a major class battle that exposed the company's union-busting efforts and the limitations of the trade union bureaucracy in defending workers' interests at that time.5
- In 1974, miners at the US Borax (later acquired by Rio Tinto) mine in Boron went on strike demanding a 25% wage increase and a one-year contract.5
- The strike lasted for nearly 5 months and was marked by violent clashes between striking miners and law enforcement/security forces brought in by the company.5
- The company took a hardline stance, hiring strike-breakers with military/police experience, setting up roadblocks, and arresting over 100 union members during the strike.5
- Pregnant striker Kay Barlow was severely beaten by police, causing her to lose her baby1.
- The International Longshore and Warehouse Union (ILWU), which represented the miners, was criticized for not providing sufficient strike funds initially and failing to shut down ports to block Borax shipments.5
- After 5 months, in October 1974, the miners were forced to accept a 3-year contract granting only half their original wage demands, ending the bitter strike.5
- The strike highlighted the militant tactics used by the company to break the union, as well as the failure of the labour leadership to fully mobilise solidarity actions in support of the Boron miners.5
The 1974 Borax strike was a major class battle that exposed the company's union-busting efforts and the limitations of the trade union bureaucracy in defending workers' interests at that time.5
Other Uses for Gerstley Borate:
Mined borates like gerstely borate, borax, fritted boron, colemanite, and ulexite have wide-ranging applications beyond the ceramics industry. Here's an overview of how boron is utilised across various industries:
Other Applications: Boron products find applications in various sectors including fibre optics, cosmetics, rubber and plastic industries, photography, explosives (e.g., pyrotechnics), petroleum-based paints, sandpaper and corrosives, composite materials, magnetic devices, advanced technological research, and embalming.
There are rumors that Gerstely Borate was purchased by the US Government by the trainload to cap underground atomic bomb testing. However, we were able to confirm that around 2009, the US Department of Energy started using boron glass and stainless steel tubes to store spent nuclear fuel under Yucca Mountain, NV. 6
- Construction and Cement: Boron-based products contribute to durable insulation materials, strengthening buildings and enhancing heat resistance, resulting in the production of lightweight and cost-effective construction materials.
- Nuclear Applications: Boron steel, boron carbide, and titanium-boron alloys are integral to atom reactors, providing high resistance to oxidation and serving as efficient neutron absorbers. They are utilised in reactor control systems, cooling ponds, and alarm shutdown systems. Additionally, colemanite aids in the storage of nuclear waste.
- Automobile Industry: Boron is employed in antifreeze production and airbags, facilitating rapid inflation upon impact. Elemental boron mixed with potassium nitrate powder is activated by electronic sensors in airbags.
- Rocket and Aviation Fuels: Boron and boron-based products serve as additives in specialised rocket and plane fuels, enhancing their performance in specific applications.
- Nanotechnology: Boron-based products are valued for their protective and endurance-boosting properties in nano-coatings, playing a significant role in the nanotechnology industry.
- Fuel Cell Research and Development: Ongoing projects aim to reduce costs associated with solid fuel production using sodium borohydride. Hydrogen, extracted from sodium borohydride through a reaction with water and borax, can be utilised in internal combustion engines or fuel cells, contributing to energy production.
Other Applications: Boron products find applications in various sectors including fibre optics, cosmetics, rubber and plastic industries, photography, explosives (e.g., pyrotechnics), petroleum-based paints, sandpaper and corrosives, composite materials, magnetic devices, advanced technological research, and embalming.
There are rumors that Gerstely Borate was purchased by the US Government by the trainload to cap underground atomic bomb testing. However, we were able to confirm that around 2009, the US Department of Energy started using boron glass and stainless steel tubes to store spent nuclear fuel under Yucca Mountain, NV. 6
FOOTNOTES
- https://digitalfire.com/material/806
- https://www.nsenergybusiness.com/projects/borax-open-pit-mine-boron-california/
- https://www.americangeosciences.org/critical-issues/faq/how-can-metal-mining-impact-environment
- https://cone6pots.ning.com/m/discussion?id=2103784%3ATopic%3A119291
- https://www.wsws.org/en/articles/2010/02/bora-f24.html
- https://d9-wret.s3.us-west-2.amazonaws.com/assets/palladium/production/mineral-pubs/boron/120401.pdf