Silica
General Information:
Chemical formula: SiO2 (silicon dioxide)
Other names: crystalline Silica (quartz), silicon dioxide (SiO2), sand, silica sand, flint, silica flour, quartz sand
Sources:
- Holcim - Silica 350 (Australia)
- Silice 200 (France)
- Sil-co-sil (United States)
- Arkansas Whetstone/Novacite (United States)
- Min-U-Sil 40 (United States)
- Solargil Silice (France)
- Bangalore Quartz (India)
-
Silica Teresa (Cuba)
Common forms:
The common geological forms of silica are quartz, cristobalite, tridymite, coesite, stishovite, lechatelierite, and different varieties of amorphous or non-crystalline silica.1
Ceramic Substitutes: soda feldspar
Silica/Quartz 2 is the most abundant mineral on earth, it is the main crystalline mineral form of silica (SiO2). Natural deposits of relatively pure quartz are plentiful and grains of it are found in many other types of rocks and in most silts, soils and clay. White or milky quartz is an opaque white, greasy-looking, sharply angular very hard rock. Pure quartz melts at 1713C, far beyond the range of an average pottery or industrial production kiln.
From a theoretical perspective, quartz is a mineral. However, in ceramics, it is also considered a material, often simply called "silica" (however original container bags often label it as "ground quartz"). Huge quantities of quartz powder are used in ceramic bodies and glazes. In bodies the quartz particles most often remain unchanged in the fired matrix, behaving as an embedded aggregate. They act as a "skeleton" in porcelain bodies. They raise the thermal expansion and make it easier to fit glazes. However, in glazes, the quartz particles dissolve in the glass and become a part of its chemical structure (thus the original properties of the quartz are gone, giving way to the new physical presence of the glass). The term "silicate" refers to minerals or fired materials where SiO2 predominates in the inventory or molecules that make up its structure. Kaolin is a silicate. In kaolin crystals, there are 2 molecules of SiO2 for every one of Al2O3. They combine chemically to form the familiar flat, stop-sign shape.
Quartz is the mineral form of silica powder used in ceramic glazes and clay bodies. It is the mineral that silica "wants to be" when cooled from molten to solid. Unlike silica glass, the quartz phase of silica is subject to inversion and accompanying volume and form change when fired through 573C. Room temperature quartz is called alpha quartz, beta quartz exists only above 573C.
Quartz sand is often used in bodies as grog for texture and to increase thermal expansion. Quartz of very fine particle size (-400 mesh) will typically enter the feldspathic melt or convert to cristobalite during firing if fluxes are lacking, coarse powdered grades help to 'squeeze' glazes into fit. Intermediate sizes (200-300 mesh) seem to be best however, since their greater surface area exerts more compressive squeeze per unit.
Quartz is also used in agriculture, paving, brick and tile, concrete, cleansers, foundry casting, paint, glass, soaps, fiberglass, electronics, plaster, sandblasting, industrial effluent filtration, drinking water filtration, hazardous waste control.
From a theoretical perspective, quartz is a mineral. However, in ceramics, it is also considered a material, often simply called "silica" (however original container bags often label it as "ground quartz"). Huge quantities of quartz powder are used in ceramic bodies and glazes. In bodies the quartz particles most often remain unchanged in the fired matrix, behaving as an embedded aggregate. They act as a "skeleton" in porcelain bodies. They raise the thermal expansion and make it easier to fit glazes. However, in glazes, the quartz particles dissolve in the glass and become a part of its chemical structure (thus the original properties of the quartz are gone, giving way to the new physical presence of the glass). The term "silicate" refers to minerals or fired materials where SiO2 predominates in the inventory or molecules that make up its structure. Kaolin is a silicate. In kaolin crystals, there are 2 molecules of SiO2 for every one of Al2O3. They combine chemically to form the familiar flat, stop-sign shape.
Quartz is the mineral form of silica powder used in ceramic glazes and clay bodies. It is the mineral that silica "wants to be" when cooled from molten to solid. Unlike silica glass, the quartz phase of silica is subject to inversion and accompanying volume and form change when fired through 573C. Room temperature quartz is called alpha quartz, beta quartz exists only above 573C.
Quartz sand is often used in bodies as grog for texture and to increase thermal expansion. Quartz of very fine particle size (-400 mesh) will typically enter the feldspathic melt or convert to cristobalite during firing if fluxes are lacking, coarse powdered grades help to 'squeeze' glazes into fit. Intermediate sizes (200-300 mesh) seem to be best however, since their greater surface area exerts more compressive squeeze per unit.
Quartz is also used in agriculture, paving, brick and tile, concrete, cleansers, foundry casting, paint, glass, soaps, fiberglass, electronics, plaster, sandblasting, industrial effluent filtration, drinking water filtration, hazardous waste control.

How it’s processed:
Silica is processed for ceramic use through several key stages:
The high purity, controlled particle size, and thermal stability of the processed silica sand make it suitable as a filler material in ceramic bodies, providing strength, reducing shrinkage, and promoting vitrification during firing of ceramic products like porcelain, tiles, and refractories.
- Crushing and Grinding: The raw silica rock or sand is first crushed using jaw or impact crushers to reduce the particle size. This is followed by grinding in a ball mill or other grinding equipment to further reduce the silica to a fine powder consistency suitable for ceramic applications.3
- Purification: Since natural silica contains impurities like iron oxides, alumina, and other minerals, it needs to be purified. Common purification methods include:
1) Washing and scrubbing to remove surface contaminants and clay particles.
2) Magnetic separation to remove iron-bearing impurities.
3) Froth flotation to separate quartz (SiO2) from other mineral impurities based on their surface properties.
4) Acid leaching with hydrochloric or sulfuric acid to dissolve metallic impurities.
The purification steps aim to increase the silica content to 99% or higher for use in ceramics and other high-purity applications.3
- Sizing and Drying: After purification, the silica is sized by screening or air classification to obtain the desired particle size distribution for ceramic bodies. Finally, the sized silica sand is dried in rotary or fluid bed dryers to remove moisture before being used in ceramic manufacturing processes.3
The high purity, controlled particle size, and thermal stability of the processed silica sand make it suitable as a filler material in ceramic bodies, providing strength, reducing shrinkage, and promoting vitrification during firing of ceramic products like porcelain, tiles, and refractories.
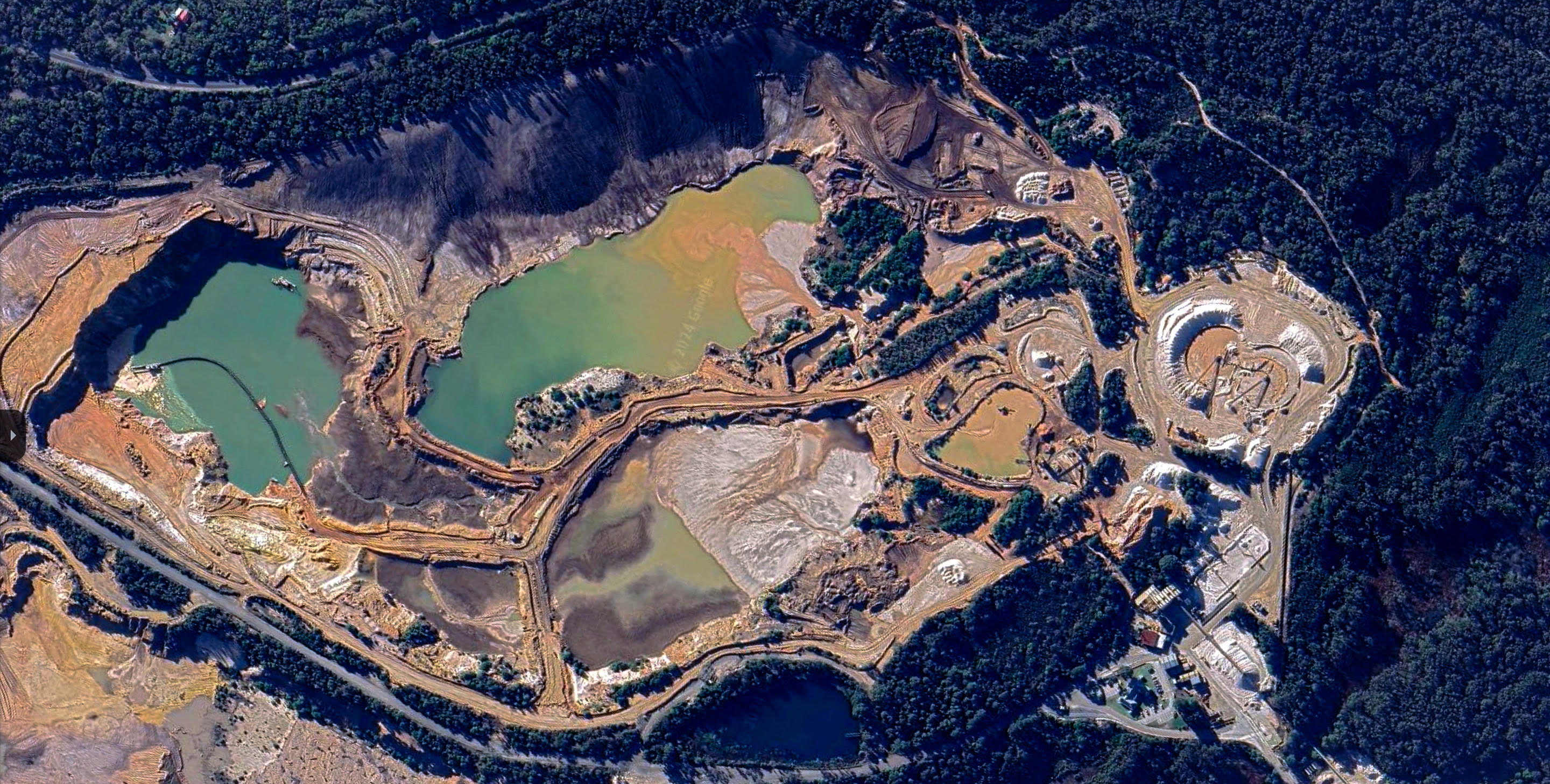
Permaculture Ethics
Earth Care
- Water Pollution: During illegal mining and refining of silica sand, excessive amounts of mud, silt, and sand can accumulate, causing water pollution in natural water bodies.4
Water is a crucial element in processing and refining silica sand. The use and potential mismanagement of water resources during these processes can lead to water pollution.5
-
Ecosystem Loss and Biodiversity Impact: Silica sand extraction often involves the destruction of local ecosystems, including natural habitats and aquatic systems, which can have a devastating impact on biodiversity.6
Open-cast silica mining can cause great damage to forests and biodiversity, as highlighted in the case of the Shankargarh region in India.5
-
Air Pollution: Silica sand extraction and processing operations can release fine silica particles into the air, which can be harmful to human health and the environment.6
-
Energy Consumption and Carbon Footprint: The extraction and processing of silica sand require significant amounts of energy, which can increase the operation's carbon footprint and contribute to climate change.6
- Atom Economy and Resource Efficiency: The dry process of silica production via flame pyrolysis has a lower atom economy (29%) compared to the wet sodium silicate process. This increases the amount of precursor (silicon tetrachloride) required per unit of silica produced, leading to higher environmental impacts.7
The search results emphasize the need for sustainable solutions, such as ecosystem restoration, energy efficiency, emission control, and recycling/reuse of silica sand, to mitigate these environmental impacts and promote responsible silica extraction and processing.
People Care
The mining, extraction, and processing of silica, especially crystalline silica, pose significant health risks to workers and communities exposed to silica dust. Prolonged inhalation of respirable crystalline silica particles can lead to silicosis, a debilitating lung disease. This risk is particularly high in the mining of silica. Additionally, silica extraction and processing can release fine particles into the air and water, posing health risks to surrounding communities and causing environmental pollution. To address these risks, proper control measures such as ventilation systems and personal protective equipment must be implemented. Furthermore, it is important that these protection procedures continue to be evaluated. In 2016, the U.S. Occupational Safety and Health Administration (OSHA) determined that workers exposed to respirable crystalline silica at previous permissible exposure limits faced a significant risk of developing silicosis and other respiratory diseases, necessitating stricter regulations to protect worker health and safety. 10
Workers have fundamental rights to safe working conditions, health protection, information, personal protective equipment, and medical surveillance to mitigate the harmful effects of silica exposure and uphold their well-being.
Workers have fundamental rights to safe working conditions, health protection, information, personal protective equipment, and medical surveillance to mitigate the harmful effects of silica exposure and uphold their well-being.
Other Uses for Silica:
Silica is used in various industries beyond ceramics. Here are some of the key sectors that utilise silica:
The search results highlight that silica's versatile properties make it an essential raw material across various industries, from glass and ceramics to metallurgy, chemicals, construction, and emerging applications in renewable energy technologies.
- Glass Industry: The main use of silica is for flat and container glass manufacture, with around 60% of each glass batch being silica sand.11 Silica is a crucial raw material for producing different types of glass products.
- Foundry Industry: Silica sand is bonded with synthetic resins to make moulds and cores for casting metals in metal foundries.11 The high melting point and thermal stability of silica make it suitable for foundry applications.
- Oil and Gas Industry: Well-rounded silica sand is used as a proppant to prop open fissures in reservoir rocks during hydraulic fracturing operations, improving permeability for oil and gas extraction.11
- Metallurgical Industry: Lump silica (quartzite) is used as a flux in metal smelting processes and as a raw material for the manufacture of ferrosilicon alloys.11
- Chemical Industry: Silica is the raw material for manufacturing various silicon compounds such as silicones, silanes, and high-purity silicon metal used in semiconductors.11
- Construction Industry: While not explicitly mentioned, silica sand is commonly used in the production of concrete, mortars, and other construction materials.
- Abrasives Industry: Silica sand is used in sandblasting and other abrasive applications due to its hardness and angular particle shape.11
- Filtration Industry: Silica is used in water filtration systems, leveraging its chemical and physical properties.11
- Renewable Energy Industry: As mentioned in 12, silica has a growing profile in the renewable energy sector, particularly in the manufacture of photovoltaic cells for solar panels.
The search results highlight that silica's versatile properties make it an essential raw material across various industries, from glass and ceramics to metallurgy, chemicals, construction, and emerging applications in renewable energy technologies.
FOOTNOTES
- https://worksafe.nt.gov.au/safety-and-prevention/crystalline-silica-and-silicosis
- https://digitalfire.com/mineral/quartz
- https://www.ftmmachinery.com/blog/silica-sand-processing-plant.html
- https://www.researchgate.net/publication/289570461_Impact_of_silica_mining_on_environment
- https://academicjournals.org/journal/JGRP/article-full-text-pdf/915EC0C53587
- https://www.geoterradominicana.com/en/articles/the-environmental-impact-of-silica-sand-extraction-and-sustainable-solutions/
- https://pubs.rsc.org/en/content/articlehtml/2023/gc/d2gc01433e
- https://www.mdpi.com/2071-1050/8/1/11
- https://journals.lww.com/imsp/fulltext/2023/14040/early_diagnosis_and_development_of_referral_system.7.aspx
- https://www.federalregister.gov/documents/2016/03/25/2016-04800/occupational-exposure-to-respirable-crystalline-silica
- https://www.energymining.sa.gov.au/industry/minerals-and-mining/mineral-commodities/silica
- https://www.australianresourcesandinvestment.com.au/2022/11/25/the-precise-world-of-silica/